A (Very) Quick History of Injection Molds
In May 1848, Henry Bewley, of the Gutta Percha Company of London, patented a process for making flexible syringes and tubes of gutta percha. He described the process as one that involved “filling a suitable mold with a substance in a granular state,” after which he would “subject these molds to a heat sufficient to liquefy the gutta percha, which on subsequent cooling will be found to retain the exact shape or figure of the molds.”¹ His company went on to make various molded and, later, extruded products, including wire coating for submarine cables. One example of his molding process is a coat of arms, pictured below, that resembled “the choicest carved or gilded oak, rosewood, or mahogany,” but was not fashioned by a skilled artist. Instead, it was manufactured “by merely pressing the ungainly lumps into a mold.” With such a mold, thousands of identical products could be manufactured “without the usual expense of artist work.” ²
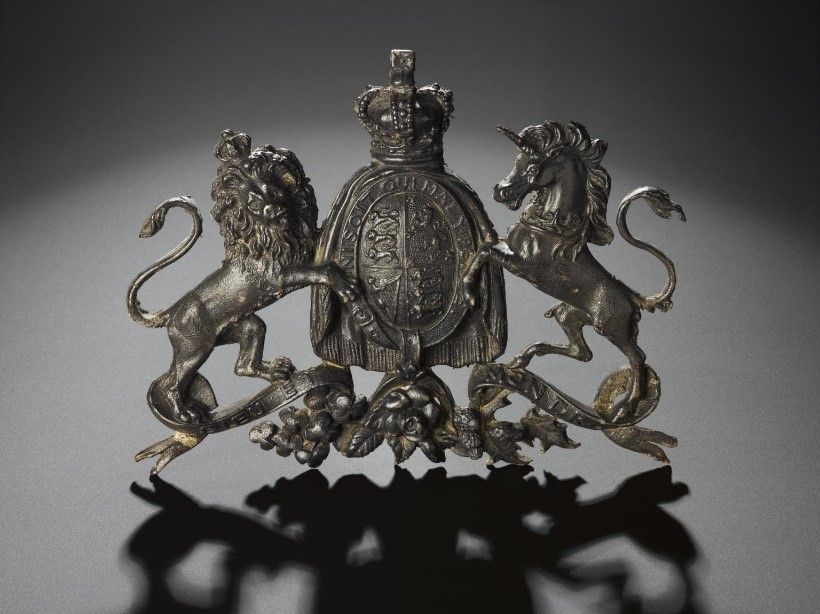
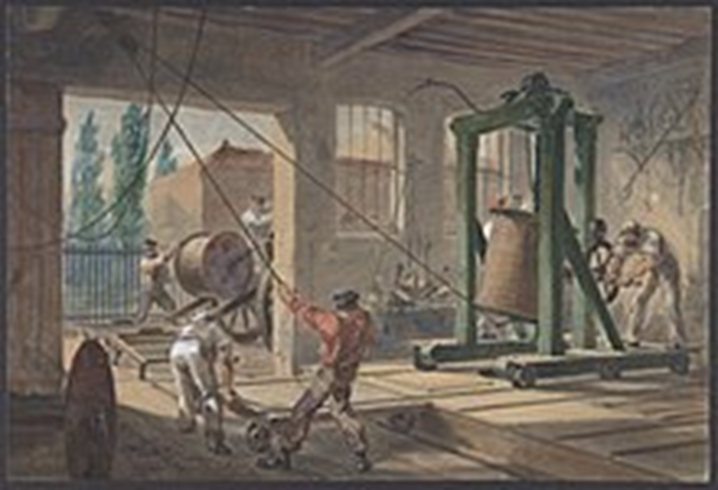
The mold in question, however, begs explanation, for although the products produced from it might number in the thousands, and while the per-part cost was accordingly reduced, still it required the expense of skilled artisans. The difference was these artisans were not artists, rather were craftspeople who came from the machining industry—now known as tool and die makers. Not to discount the necessary components of both material and molding machine, but the heart of that molding process lies in the mold, the history of which is more difficult to trace than the machines used to inject it. Casting and molding may share a common ancestor from the distant past, one that extends back roughly five thousand years, but for our purposes the high speed, repeatable, and high-volume molding process is relatively new. It too, seems to owe its origin to the gutta percha revolution, because in 1846, Charles Hancock, also of the Gutta Percha Company, published an English patent, no. 11,208, that described the mold in detail, including vents for outgassing entrapped air and a method of injecting air for blow molding.⁵
Those machinists, who in this case remain unnamed, formed part of a class of workers who could trace their origins back only a couple of generations, back to John Wilkinson’s cannon-boring machine, first patented in 1774, which vastly improved the accuracy of the bore. Upon ordering one of James Watt’s steam engines, Wilkinson came to realize that the cylinders
utilized in Watt’s engine suffered from the same deficiencies as the Admiralty’s cannon, namely, an appalling lack of precision. So, for the cylinder utilized in his steam engine, he adapted his boring machine to Watt’s thirty-six-inch cylinder blank, chaining it down and then ratcheted forward his rotating boring tool. He achieved an accuracy of .010”, which was stunning for his time, spawning the concept of precision-machining and spurring the development of machine tools. Wilkinson’s boring machine was just one of several contemporaneous inventions that formed the basis of the precision industry—the lathe, precision screw, and dividing engine being among the others. Failure may be an orphan, in this case however, the steady growth of precision machining has multiple fathers—Jesse Ramsden, who invented a screw-making machine and also perfected a dividing engine that scribed exact divisions onto brass mural circles for use by astronomers, and Henry Maudslay, whose iron lathe improved the accuracy of machined parts by an order of magnitude, and whose micrometer, named the “Lord Chancellor,” was capable of measuring down to .001”.⁶
None of this happened outside its social context. All across Great Britian small, often one-family shops opened, first making clocks, then instruments of various kinds, usually in brass. They gave rise to larger organizations, like Bewley’s gutta percha company, all of which profited from a steady demand for their products.⁷ So successful were those shops that the Danes, by the end of the century, sought to duplicate them in Denmark, while the Americans, led by Francis Cabot Lowell and Thomas Attwood Digges, stole, replicated, and recruited British technology over a period of decades in the late eighteenth or early nineteenth centuries.⁸ Denmark, with its small population and scant resources, never developed into a machining powerhouse. But here in the US, with its abundant resources and constantly swelling population, the industry soon matched, then overtook the British in machine development.
And just as the small, often family-based British machining companies found in the midlands a quarter-millennia ago flourished and grew, so too dd their heirs—the small, often family-based mold-makers or molders of the mid twentieth century in the US. From a tiny beginning in 1929, the sixty or so independent molders here grew to 434 today. The common trait shared by these early adopters was their ability to manufacture their own molds and develop their own technology.⁹ The growth of the independent contract molders, a number that does not include those captive operations inside larger concerns, bears witness to the constant improvement of our industry over time.¹⁰ Today over 33,000 people are involved in the plastics industry that produces over 16 billion dollars of exports in North Carolina alone. They were, and are, the principal reason that The Polymers Center exists, and will continue to serve them through their mission to “support, maintain, and encourage” our industry.
Footnotes:
¹ US Patent Office, Patent no. 5589, May 23, 1848. The patent literature is extensive. See, Eugene F. A. Obach, “Gutta Percha,” Journal for the Society of Arts, [XLVI (January 1898): 169-197.
² David Bartlett, London by Day and Night; or, Men and Things in the Great Metropolis, (New York: Hurst & Company, 1852), 58.
³ https://collection.sciencemuseumgroup.org.uk/objects/co9687/gutta-percha-armorial-moulding-1850-1900-coat-of-arms
⁴ https://thedailygardener.org/ota20200704/
⁵ J. L. White, “Pioneers of Polymer Processing Charles Hancock—The First Thermoplastics Processing Innovator”, International Polymer Processing XIII (1998): 230. https://www.degruyter.com/document/doi/10.3139/217.980230/html?lang=en
⁶ Simon Winchester, The Perfectionists: How Precision Engineers Created the Modern World, (New York: Simon and Schuster, 2018), 50-52, 74-78.
⁷ A. D. Morrison-Low, Making Scientific Instruments in the Industrial Revolution, (London: Routledge, Taylor & Francis Group, 2007), 36-46.
⁸ https://www.history.com/news/industrial-revolution-spies-europe
⁹ Jeffey L. Meikle, American Plastic, A Cultural History (New Brunswick: Rutgers University Press, 1995), 92-98.
¹⁰ https://www.ibisworld.com/industry-statistics/number-of-businesses/contract-injection-molding-manufacturing-united-states/
CONTACT US TO LEARN MORE: 704-602-4100